Hydrogen Peroxide Gas Plasma
The fastest process to bring your product to market
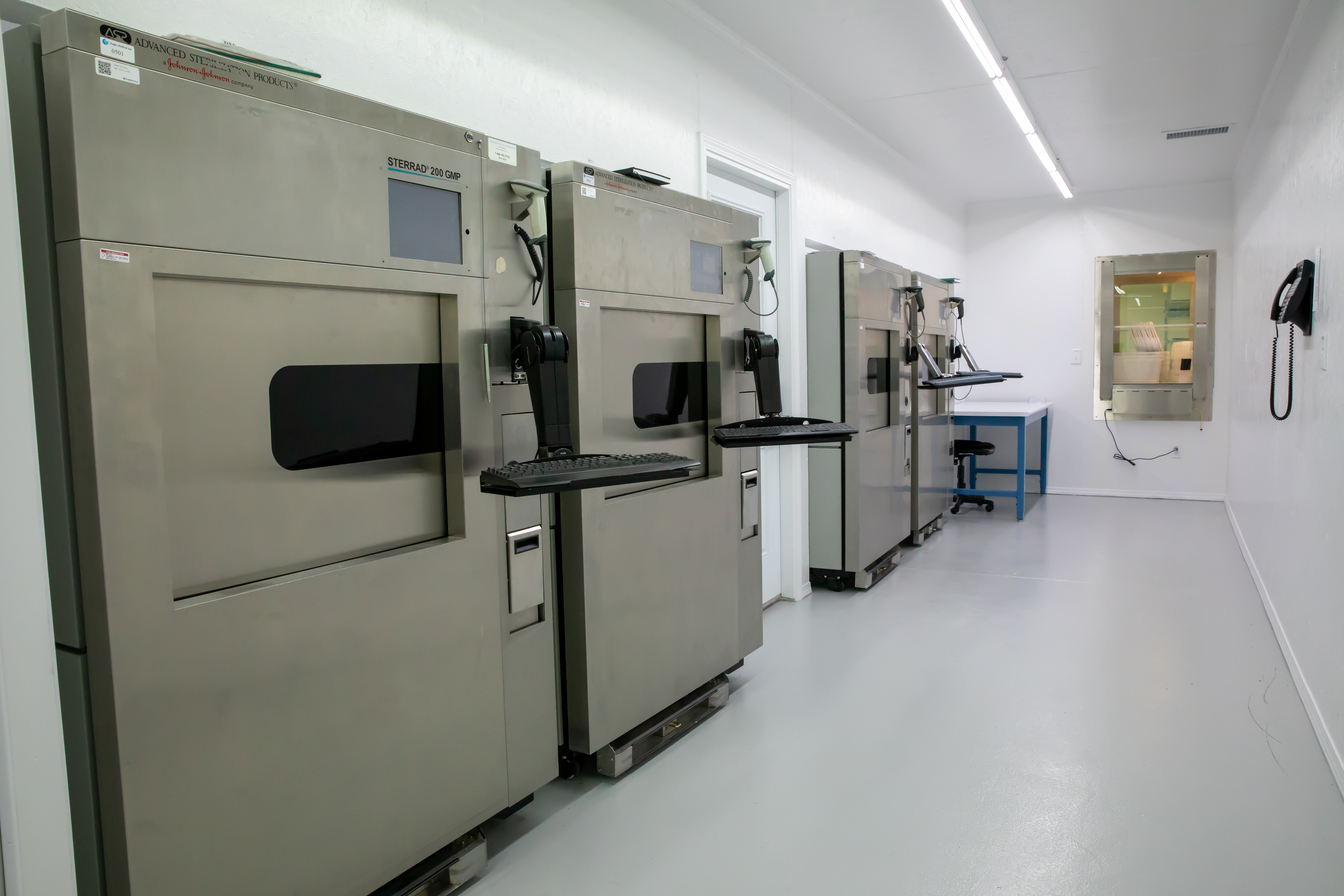
Hydrogen Peroxide Gas Plasma Sterilization (HPGP) provides a low temperature and environmentally friendly sterilization process that is commonly used to sterilize orthopedic implants and pre-filled syringes, as well as self powered and programmable electronic devices in a timely and cost-effective manner.
The FDA now recognizes HPGP as an "Established form of sterilization, Category A":
These are methods that have a long history of safe and effective use as demonstrated through multiple sources of information such as
ample literature, clearances of 510(k)s or approvals of premarket approval (PMA) applications, and satisfactory QS inspections. For established methods such as dry
heat, EO, steam, radiation, and vaporized hydrogen peroxide, there are voluntary consensus standards for development, validation, and routine control that are
recognized by FDA.
Examples of these Established Category A Sterilization Methods:
• Dry heat
• EO with devices in a fixed, rigid chamber
• Moist heat or steam
• Radiation (e.g., gamma, electron beam)
• Vaporized Hydrogen Peroxide (H2O2 )
"EtO use appears to have diminished in favor of HPGP which affords higher throughput and minimal regulatory constraints" (Boiano and Steege, 2015)
HPGP PresentationMechanism of Action
A strong oxidizer, concentrated H2O2 oxidizes organic material fairly readily on it's own. To increase the speed and effectiveness though, during an HPGP cycle, a vacuum is pulled on the chamber and a strong electrical field is applied. This generates a gas-plasma of microbicidal free-radicals (e.g. hydroxyl and hydroperoxyl) that more efficiently neutralizes any would-be contaminants.
Once the sterilization cycle completes, the chamber is vented through a catalytic converter, breaking down any residual H2O2 and free radicals into water and oxygen.
Benefits
- Non-toxic residuals (H2O and O2) & safe for the environment
- Post-aeration of residuals is not necessary
- Short cycle times ( ≈ 2 hrs )
- Low operating temperatures ( < 55°C )
- High material compatibility and compatibility with materials not offered by other forms of sterilization (refer to our Material Compatibility Chartfor details)
Limitations
-
Incompatible with some materials such as:
- biological materials (natural rubber, cellulose, cotton, linen, silk, wool, etc.)
- biologics (proteins)
- large amounts of copper or brass.
- Cannot sterilize liquids; liquids must be sterilized and sealed prior to exposure or added after HPGP sterilization cycle
HPGP 200 GMP Sterilization Systems
Our HPGP sterilization systems are run and maintained in-house to prevent downtime and ensure timely product delivery.
Specifications
- Chamber Volume ≈ 270 liters (150 liters of payload)
- Cycle Time ≈ 2 hrs.
- Operating Temps < 55°C
- Biological Indicator Readout: 24 hrs.
- Product turnaround time: 48-72 hrs.
Does the FDA Recognize H2O2 Sterilization as a valid process for medical products?
Yes, the FDA has categorized Hydrogen Peroxide (H2O2) as an "Established form of sterilization, Category A", which means it is easily used in any form of 510(k) submission process with the FDA, where compatible with your device. Download the FDA letter that documents it here.
How does the cost of H2O2 Sterilization compare with EO and Radiation?
H2O2 is quite competitive for market volumes of 1MM units or less annually when compared to EO and irradiation at low to medium volume processing. The graph below gives a basic idea of the 2021 cost comparisons that are relevant during early stage considerations of competing sterilization methods for a typical device that is less than 6"x6"x6" in overall size:
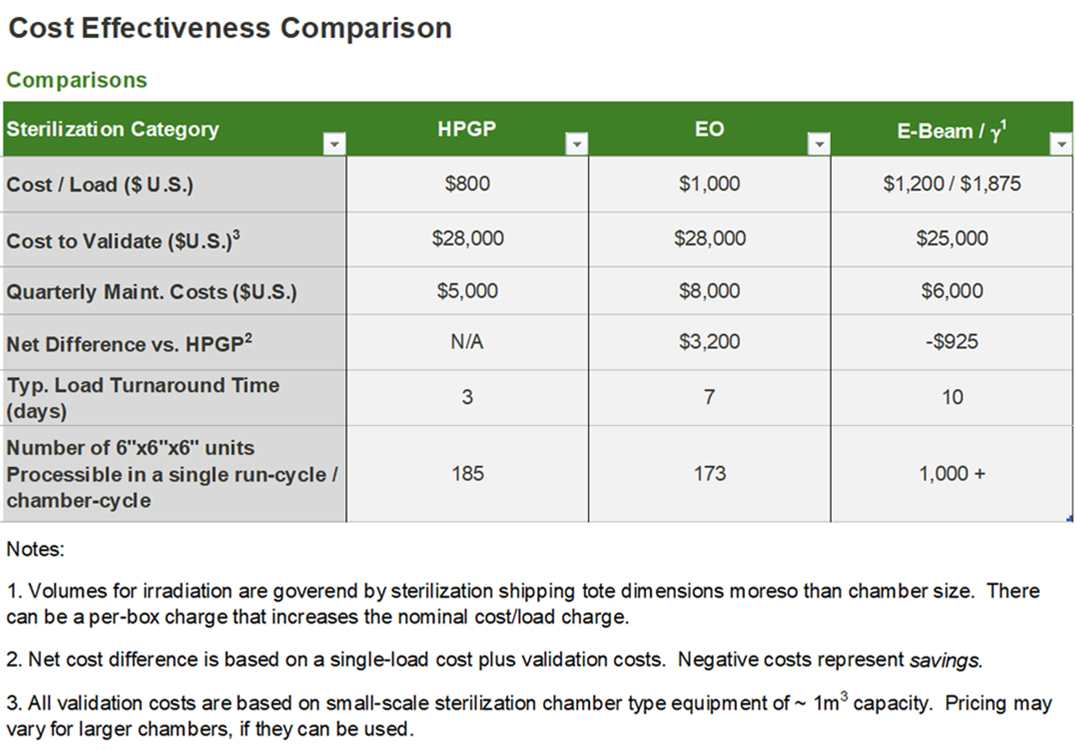
How fast can I process devices compared to EO?
Turnaround time is an essential variable when considering the appropriate sterilization method for your product and, with low to medium processing volumes, HPGP is quite competitive. The graph below shows comparisons for typical turnaround times for the industry standard processes:
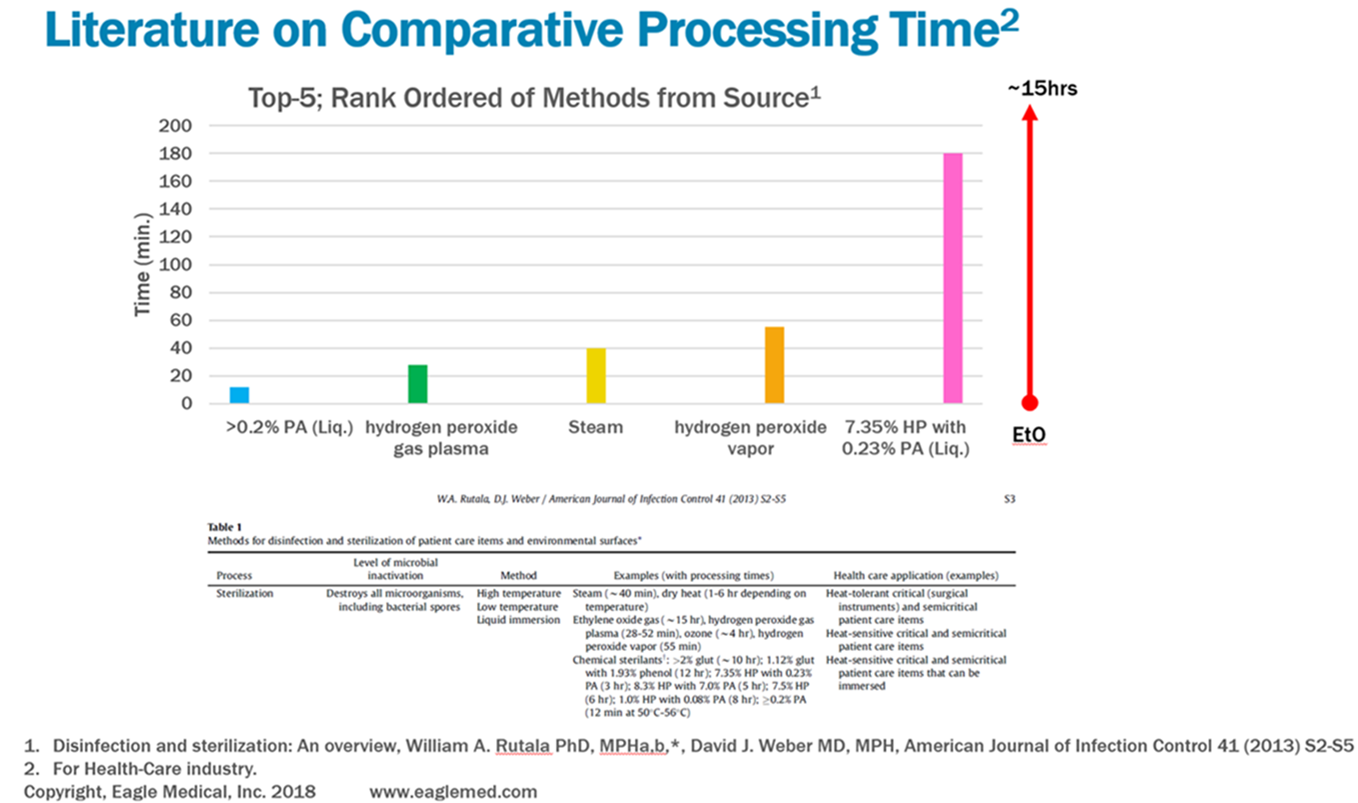
I have designed the packaging for my device to be compatible with EO sterilization, can I use the same packaging materials, or do I need to re-qualify them for HPGP?
You can likely use the same packaging that was used with EO. In most cases standard Tyvek or similar breathable microbial barriers that are of non-cellulose construction and PET/PETG film based, mated pouches are compatible with HPGP sterilization. If you are uncertain, please send us your pouch material data-sheets with your quote request and we will evaluate them for compatibility.
Are all transparent films that are used in pouch construction compatible with HPGP sterilization?
No. Those films that are laminated in layers with water-based primers are incompatible. Check your material specifications for how the film side of your pouches are constructed in order to be sure, or reach out to us for help with packaging evaluation.
Can I process a cannulated device effectively with HPGP?
Yes, but there are limits. HPGP sterilization is a surficial form of sterilization and the sterilant is unable to pass through non-porous films. A good rule to go by is; cannulae of less than 3mm diameter and length greater than 10cm are too small for effective sterilization via HPGP. If your device is near these limits, reach out to us to learn how we can perform some simple tests to determine if your device is a good candidate for HPGP sterilization.
From Product to Production
Throughout the process of bringing your product to market, Eagle Medical is committed to providing you with support to ensure ease of compliance with all FDA and ISO regulations.
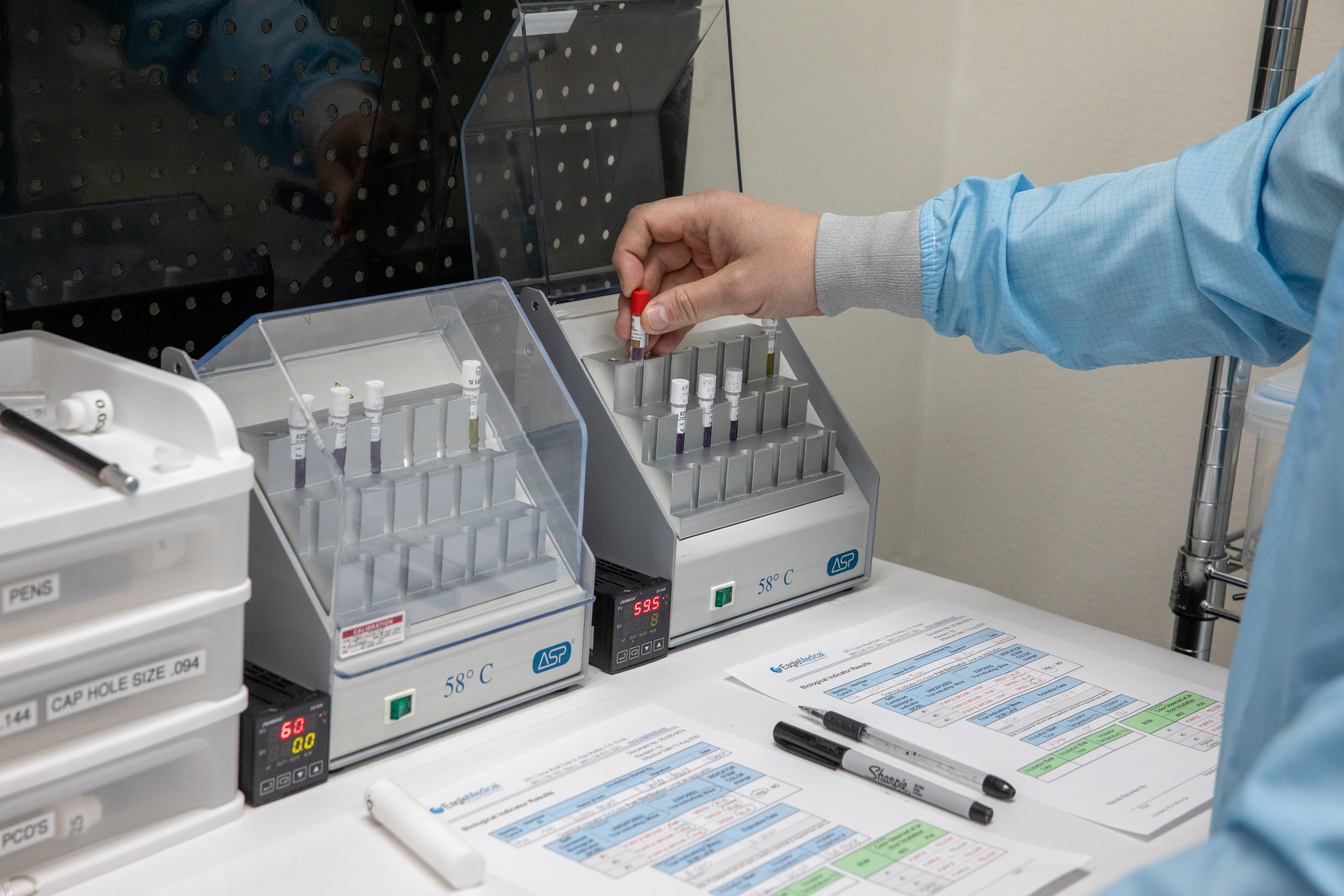
-
Feasibility Studies - We work with you to determine if HPGP is the right method of
sterilization for your product.
- Packaging Materials Viability
- Product Exposure Testing
-
Cycle Development - A full cycle development project is completed for your product
to ensure efficacy of the sterilization process
- Process Challenge Devices - use of PCDs ensure sterilization effectiveness of production cycles